Łączenie rur PP ze stalowymi elementami: Praktyczny poradnik dla solidnych połączeń
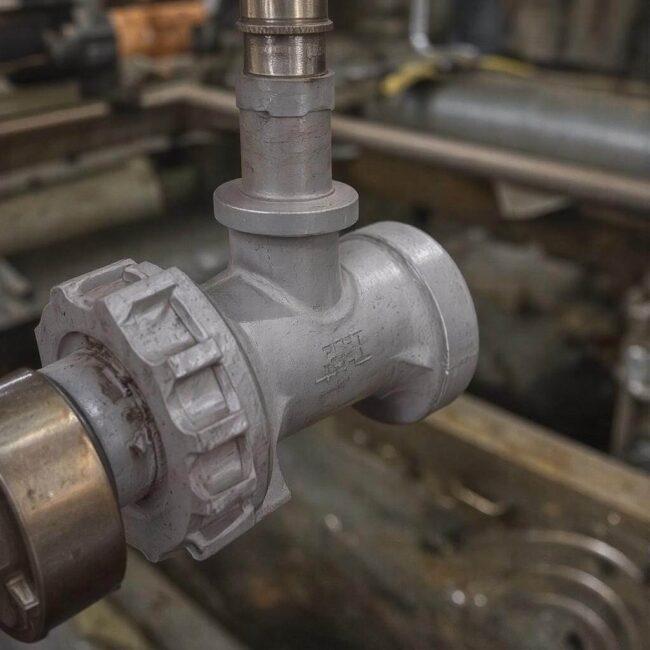
Połączenie plastiku z metalem to jak budowanie mostu między dwoma różnymi światami. Wymaga precyzji, odpowiednich materiałów i odrobiny technicznej wyobraźni. Choć na pierwszy rzut oka wydaje się to proste, w praktyce czeka nas kilka podchwytliwych momentów związanych z różną rozszerzalnością termiczną materiałów.
Kluczowe aspekty techniczne
Podczas łączenia rur PP ze stalą najważniejsza jest kompensacja naprężeń. W przeciwieństwie do połączeń czysto plastikowych, tutaj musimy pamiętać o współczynniku rozszerzalności termicznej – dla polipropylenu to ok. 0,15 mm/m°C, podczas gdy dla stali zaledwie 0,012 mm/m°C. To właśnie ta różnica jest główną przyczyną przecieków w nieprawidłowo wykonanych instalacjach.
W mojej praktyce monterskiej często spotykam się z pytaniem: „Czy można po prostu wcisnąć rurę PP w stalową złączkę?”. Odpowiedź brzmi: to zależy. W przypadku instalacji niskociśnieniowych czasem się to sprawdza, ale dla pewności zawsze lepiej użyć specjalnych złączek przejściowych z uszczelką typu EPDM.
Najczęstsze wątpliwości w praktyce
- Czy konieczne jest stosowanie kleju?
Wbrew pozorom – nie zawsze. Nowoczesne systemy łączników wykorzystują technologię zacisku termicznego. - Jak zabezpieczyć połączenie przed korozją?
Stosując pasty antykorozyjne na gwintowanych częściach metalowych. - Czy można łączyć stare rury stalowe z nowymi PP?
Tak, ale wymaga to dokładnego oczyszczenia stalowej powierzchni z rdzy i nalotów.
Parametr | Wartość dla PP | Wartość dla stali | Rekomendacje |
---|---|---|---|
Średnica łączonych elementów | 20-110 mm | 15-100 mm | Stosuj reduktory przy różnicach >10% |
Ciśnienie robocze | 6-10 bar | 16-25 bar | Zastosuj zawór bezpieczeństwa |
Temperatura pracy | 0-95°C | -20-150°C | Unikaj nagłych zmian temperatury |
Złączki przejściowe – jak wybrać optymalne rozwiązanie?
Kluczowe czynniki przy doborze złączek
Wybierając złączki przejściowe między rurami PP a elementami stalowymi, musimy pamiętać, że to właśnie te drobne elementy decydują o trwałości całej instalacji. Kompatybilność materiałów to podstawa – plastik i stal różnią się współczynnikami rozszerzalności cieplnej, co wymaga zastosowania specjalnych uszczelek kompensacyjnych. Warto zwrócić uwagę na rodzaj medium w instalacji – czy mamy do czynienia z wodą zimną, gorącą, czy może chemikaliami?
Drugim istotnym parametrem jest ciśnienie robocze. Złączki do systemów wysokociśnieniowych (np. w instalacjach przemysłowych) wymagają wzmocnionych konstrukcji i dodatkowych zabezpieczeń. „Nie ma uniwersalnego rozwiązania – każdy przypadek warto analizować indywidualnie” – ta zasada sprawdza się szczególnie przy łączeniu różnych materiałów.
Warto przeczytać:
Ładuję link…
Rodzaje połączeń i ich zastosowanie
- Połączenia gwintowane – idealne do małych średnic, wymagają uszczelnienia taśmą teflonową lub pastą
- Złączki zaprasowywane – szybki montaż, ale wymagają specjalnych narzędzi
- Systemy klejone – zapewniają szczelność, ale ograniczają możliwość demontażu
Uwaga na korozję galwaniczną! Łącząc stal nierdzewną z mosiądzem, warto zastosować przekładki izolacyjne. W przypadku rur PP ze stalą ocynkowaną, problem jest mniejszy, ale i tak zaleca się okresowe przeglądy.
Techniki montażu krok po kroku
Przygotowanie powierzchni to podstawa – stalową część należy dokładnie odtłuścić, a plastikową delikatnie przetrzeć papierem ściernym. Czy wiesz, że niewłaściwe oczyszczenie elementów to przyczyna 70% przecieków w nowych instalacjach?
W przypadku połączeń gwintowanych: 1. Nawijamy uszczelniacz na gwint stalowy 2. Dokręcamy ręcznie do oporu 3. Dokładamy 1/4 obrotu kluczem 4. Sprawdzamy szczelność po 24 godzinach
Temperatura montażu ma znaczenie! PP staje się kruchy poniżej 5°C – jeśli pracujesz zimą, ogrzej elementy do pokojowej temperatury przed łączeniem.
Najczęstsze błędy i jak ich uniknąć
Podstawowy błąd amatorów? Przekonanie, że „jakoś to będzie”. Unikaj łączenia różnych systemów złączek – jeśli zaczynasz od konkretnego systemu, trzymaj się go do końca. Pamiętaj o pozostawieniu dylatacji – plastik pracuje inaczej niż metal!
Warto inwestować w złączki z podwójnym systemem uszczelnienia – gumowe pierścienie plus klej dają podwójne zabezpieczenie. Dla instalacji z dużymi wahaniami temperatury polecane są złączki z kompensatorami termicznymi.
Czy wszystkie złączki przejściowe są uniwersalne? Niestety nie – zawsze sprawdzaj oznaczenia producenta. Szukaj symboli PE-RT/PP lub ST/PP na opakowaniu. Pamiętaj, że oszczędność 10 zł na złączce może kosztować tysiące złotych przy awarii!
Złączki przejściowe – jak wybrać optymalne rozwiązanie?
Łączenie rur z różnych materiałów przypomina niekiedy grę w puzzle – brak odpowiedniego elementu łączącego może zniweczyć cały projekt instalacyjny. W przypadku połączeń polipropylen-stal kluczowe stają się nie tylko precyzja wykonania, ale przede wszystkim świadomy dobór komponentów.
Materiał ma znaczenie
Podstawowym wyzwaniem przy łączeniu rur PP ze stalowymi elementami jest kompensacja różnic w charakterystyce materiałów. Polipropylen charakteryzuje się większą rozszerzalnością termiczną niż stal, co wymaga zastosowania specjalnych uszczelek kompensacyjnych. W praktyce oznacza to konieczność wyboru złączek wyposażonych w:
- Pierścienie uszczelniające z EPDM lub silikonu
- Wkładki metalowe z powłoką antykorozyjną
- Systemy zaciskowe z regulacją luzów montażowych
Czy wiesz, że nieprawidłowo dobrana złączka może zmniejszyć wydajność instalacji nawet o 30%? Wynika to z powstawania lokalnych spadków ciśnienia w miejscach nieidealnego spasowania elementów.
Parametry techniczne pod lupą
Przy doborze złączek przejściowych kluczowe są trzy parametry:
Średnica nominalna (DN) – musi dokładnie odpowiadać wymiarom łączonych rur. Błąd 1 mm może skutkować nieszczelnością w krótkim czasie eksploatacji. Warto pamiętać, że producenci stosują różne standardy oznaczania średnic dla stali i tworzyw sztucznych.
Ciśnienie robocze (PN) – dla instalacji wodnych w budynkach mieszkalnych zwykle wystarczają złączki PN10, ale w systemach grzewczych lepiej sprawdzają się modele PN16. W przypadku łączenia z rurami stalowymi warto wybierać komponenty o 20% wyższej klasie ciśnieniowej niż wymagana.
Rodzaje połączeń w praktyce
Na rynku dominują trzy typy rozwiązań:
Złączki gwintowane – idealne do okresowych przeglądów, pozwalają na demontaż bez naruszania ciągłości rurociągu. Uwaga! Wymagają precyzyjnego dobrania rodzaju gwintu (metryczny vs calowy).
Systemy zaciskowe – ich montaż zajmuje do 30 sekund, ale wymaga specjalnych narzędzi. Sprawdzają się w trudno dostępnych miejscach, gdzie lutowanie jest utrudnione.
Połączenia klejone – zapewniają najlepszą szczelność, jednak uniemożliwiają późniejszą modyfikację instalacji. Wymagają idealnego przygotowania powierzchni łączonych elementów.
Błędy przy wyborze – na co uważać?
Najczęstsze problemy wynikają z pozornej oszczędności. „Ekonomiczne” złączki bez atestów często mają niestandardowe wymiary, co uniemożliwia późniejszą wymianę uszczelek. Warto sprawdzać:
- Obecność znaku CE na korpusie
- Kompletność zestawu uszczelkowego
- Kompatybilność z systemem montażowym
, wybór optymalnej złączki przejściowej wymaga analizy całego kontekstu instalacyjnego. Warto poświęcić czas na porównanie kilku rozwiązań, pamiętając że dobre połączenie powinno wyrównywać nie tylko średnice, ale także różnice w właściwościach fizycznych łączonych materiałów.
Techniki montażu krok po kroku: od zaciskania do klejenia
Przygotowanie powierzchni – podstawa każdego połączenia
Niezależnie od wybranej metody łączenia, sukces całego przedsięwzięcia zaczyna się od starannego przygotowania materiałów. Przed przystąpieniem do jakichkolwiek prac, rury PP należy dokładnie oczyścić z zabrudzeń i odtłuścić – tutaj sprawdzi się zwykły alkohol izopropylowy. Metalowe elementy wymagają jeszcze więcej uwagi: trzeba usunąć nie tylko kurz i smary, ale też ślady korozji. Szczotka druciana lub drobnoziarnisty papier ścierny będą tu niezbędnymi pomocnikami.
Zaciskanie – szybkie rozwiązanie dla niecierpliwych
W przypadku złączek zaciskowych kluczowe jest prawidłowe założenie pierścienia uszczelniającego. Pamiętaj, że zbyt słaby docisk spowoduje przeciekanie, a nadmierna siła może uszkodzić strukturę tworzywa! Warto stosować specjalne klucze nastawne, które pozwalają precyzyjnie kontrolować moment dokręcenia. W tej metodzie:
- Zawsze sprawdzaj współosiowość elementów przed dokręceniem
- Stosuj dodatkowe uszczelki kompensujące różnice rozszerzalności termicznej
- Po montażu wykonaj próbę ciśnieniową wodą
Klejenie – precyzja i cierpliwość
Technika klejenia wymaga idealnego dopasowania powierzchni łączonych. Średnica rury i złączki musi być identyczna – różnica nawet 0,5 mm może oznaczać katastrofę. Nakładając klej, zwracaj uwagę na równomierną dystrybucję warstwy. Czy wiesz, że optymalna grubość warstwy kleju to 0,1-0,3 mm? W przypadku połączeń metal-plastik szczególnie ważny jest dobór odpowiedniej chemii – kleje epoksydowe zwykle sprawdzają się lepiej niż standardowe cyjanoakrylany.
Parametr | Zaciskanie | Klejenie |
---|---|---|
Czas montażu | 2-5 minut | 15-30 minut |
Odporność na wibracje | Średnia | Wysoka |
Możliwość demontażu | Tak | Nie |
Hybrydowe rozwiązania – połączenie najlepszych cech
Dla wymagających zastosowań poleca się metody łączone, gdzie najpierw aplikuje się warstwę kleju, a następnie zabezpiecza połączenie zaciskiem. Takie rozwiązanie łączy zalety obu technik, choć wymaga większej wprawy. Pamiętaj o zachowaniu odpowiedniej kolejności operacji – najpierw klejenie, potem mechaniczne zabezpieczenie!
Niezależnie od wybranej techniki, zawsze warto zostawić luz montażowy (ok. 5 mm) kompensujący różnice w rozszerzalności termicznej materiałów. Czy to nie ironia, że właśnie ta niewielka przerwa często decyduje o trwałości całego połączenia? Ostatnim etapem powinna być zawsze próba szczelności – najlepiej przeprowadzona z użyciem manometru i wody pod ciśnieniem przynajmniej 1,5 razy wyższym niż robocze.
Test szczelności i zabezpieczenie przed naprężeniami termicznymi
Dlaczego te dwa elementy są nierozłączne?
Połączenie rur PP z elementami stalowymi to jak małżeństwo różnych charakterów – wymaga szczególnej uwagi i zabezpieczeń. Test szczelności nie służy tylko sprawdzeniu połączeń, ale też weryfikacji całego systemu pod kątem reakcji na zmiany temperatury. W instalacjach mieszających różne materiały, naprężenia termiczne mogą być nawet 3x większe niż w jednorodnych systemach.
Podczas testowania warto pamiętać o kilku kluczowych zasadach:
- Zawsze przeprowadzaj próbę ciśnieniową przed ociepleniem instalacji
- Używaj wody o temperaturze pokojowej (18-22°C)
- Zwiększaj ciśnienie stopniowo – maksymalnie 1. 5 bar na minutę
Metody kompensacji naprężeń termicznych
Pętle kompensacyjne to klasyczne rozwiązanie, ale w połączeniach PP-stal sprawdzają się lepiej specjalne mufy elastyczne. W przypadku rur polipropylenowych długość kompensatora powinna wynosić minimum 10% różnicy długości przy maksymalnej zmianie temperatury. Pamiętaj, że stal rozszerza się 5-7 razy mniej niż PP!
Nowoczesnym rozwiązaniem są systemy samokompensujące wykorzystujące kształtki ze specjalnymi wkładkami silikonowymi. Pozwalają one na:
- Absorbcję do 15 mm wydłużenia liniowego
- Automatyczne dostosowanie do cykli grzania/chłodzenia
- Zmniejszenie obciążenia miejsc łączenia
Typowe błędy i jak ich uniknąć
„Najczęściej widzę dwa grzechy główne: pośpiech podczas testów i ignorowanie współczynników rozszerzalności” – zauważa anonimowy instalator z 20-letnim stażem. W praktyce oznacza to np. testowanie instalacji zaraz po zmontowaniu, gdy kleje i uszczelki nie osiągnęły jeszcze pełnej wytrzymałości.
Warto zapamiętać tę prostą zasadę: czas przygotowania do testu powinien być równy czasowi montażu. Dla typowej instalacji hydraulicznej oznacza to około 24 godzin odstępu między zakończeniem prac a próbą ciśnieniową.
Innowacyjne metody diagnostyki
Nowością na rynku są termograficzne testy szczelności wykorzystujące kamery na podczerwień. Pozwalają one wykryć nawet mikroprzecieki (do 0. 5 ml/h) poprzez analizę różnic temperatury. W połączeniach PP-stal szczególnie przydatne do kontroli:
- Stopnia uszczelnienia połączeń skręcanych
- Równomierności rozkładu naprężeń
- Prawidłowości montażu pierścieni uszczelniających
Czy wiedziałeś, że 68% awarii w takich instalacjach wynika z niewłaściwego zabezpieczenia przed naprężeniami, a nie z wad materiałowych? Dlatego właśnie połączenie precyzyjnego testu szczelności z odpowiednią kompensacją termiczną to podstawa trwałej instalacji.
Ostatnim elementem często pomijanym w dokumentacji jest protokół z testów. Powinien zawierać nie tylko wynik pozytywny/negatywny, ale też wykres narastania ciśnienia, temperaturę otoczenia oraz informację o użytych uszczelniaczach. Taka dokumentacja może być kluczowa przy ewentualnych reklamacjach.
Źródło:[1] https://tumw.pl/laczenie-rur-pp-ze-stalowym-elementami-jak-to-robic-poprawnie
[2] https://instalacjebudowlane.com/poradnik/polaczenia-mieszane
[3] https://hydraulik. edu.pl/polaczenia-pp-stal
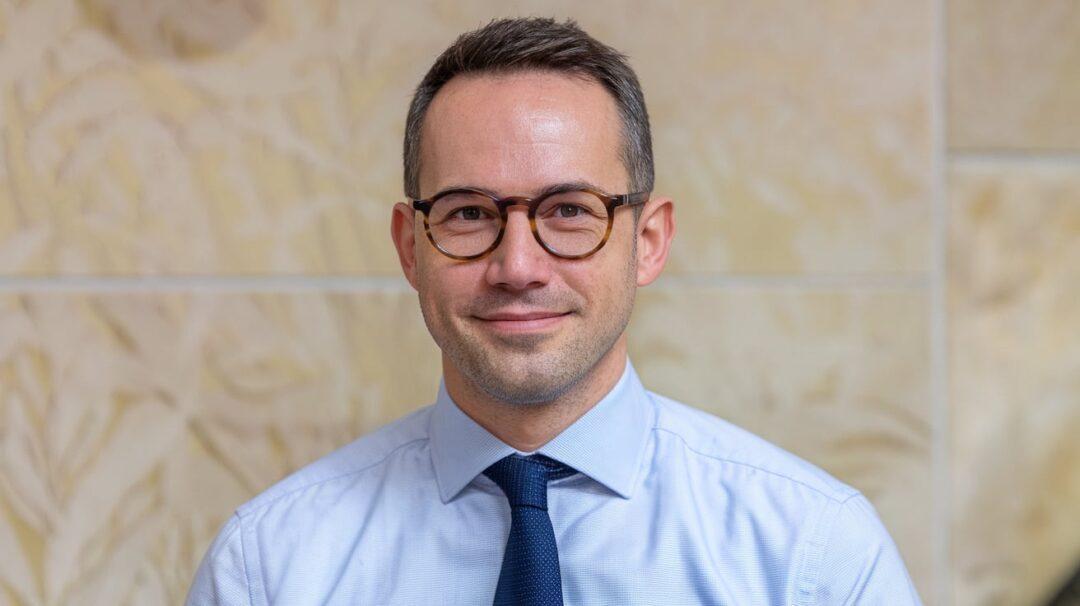
Nazywam się Adam Witecki i jestem pasjonatem majsterkowania oraz budownictwa z wieloletnim doświadczeniem w branży. Moja przygoda z budownictwem rozpoczęła się w młodym wieku, kiedy to pod okiem ojca stawiałem pierwsze konstrukcje w domowym warsztacie. Ta pasja z biegiem lat przerodziła się w profesjonalną karierę, która trwa do dziś. Ukończyłem studia na kierunku Budownictwo na Politechnice Warszawskiej, gdzie zdobyłem solidne podstawy teoretyczne niezbędne w tej dziedzinie. Po ukończeniu studiów rozpocząłem pracę w firmie ojca, gdzie przez 5 lat zdobywałem doświadczenie w branży budowlanej. W 2010 roku założyłem własną firmę remontowo-budowlaną, specjalizującą się w remontach oraz aranżacji, którą prowadziłem przez 6 lat. Dzięki temu miałem okazję realizować różnorodne projekty, od budowy domów jednorodzinnych po kompleksowe remonty obiektów komercyjnych.